Pharmaceutical Machinery
Verkora is working together with Manufacturers to supply and export the demand for Granulation Section, Tablet Compression, Filling and Packing Machinery for Pharmaceutical, Nutraceutical and Cosmeceuticals Industries.
At Verkora, delivering more than just products is our commitment. We focus on excellence in the manufacturing process to ensure the highest standards, backed by 35 years of extensive experience through our trusted manufacturing partners. Your satisfaction is our top priority, and we strive to meet your unique requirements with precision and care.
From pharma colleges and laboratories to API manufacturers, pharmaceutical companies, and Ayurveda producers, countless organizations trust us to deliver reliable, high-quality equipment. Our machinery is crafted using superior materials, advanced technologies, and meticulous attention to detail. We never compromise on quality, ensuring each product meets the rigorous standards our customers expect.
What sets Verkora apart is our unwavering dedication to excellence. Beyond fair pricing and exceptional products, we take extra measures to guarantee top-notch quality and performance. With a commitment to your satisfaction, we go above and beyond to ensure our machinery empowers your business with precision, reliability, and results you can count on.
Tablet Compression Machinery
Ancillary Equipment
FLUID BED DRYER (FBD)
Fluid bed dryers, as their name suggests, are used for drying materials such as granules, tablets, powders, fertilizers, and plastics.
Fluid bed dryers work on the principle of fluidization, a process where a material is converted from a static solid-like state to a dynamic fluid-like state. In this process, hot gas or air is introduced through a perforated distribution plate into the area holding the material. This hot gas pumps through the spaces between solid particles. As the velocity of the gas or air increases, the upward forces on the particles increase, causing them to equal the gravitational forces below.
This creates a state of fluidization where the particles are suspended in what appears to be a boiling bed of liquid. What once moved in a solid way can now flow like water. Each particle is in direct contact with, and surrounded by, the hot gas or air – creating an efficient and uniform drying process.
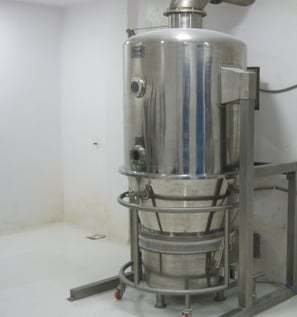
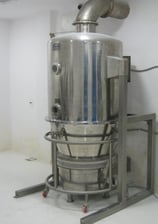
The Fluid Bed Dryer unit is made in two pieces, from S.S. 304 grade steel.
External surfaces of the dryer, all non-contact / sight parts, and all contact parts have super glossy Mirror finish built from S.S. 304.
The Crevice free profiles both inside and outside to prevent material Entrapment at all welds.
The second unit called the Expansion chamber made from S.S. 304 / 316 and it contains Filter Finger Bags.
Retarding Chamber made of S.S. 304 is locked with Expansion chamber by means of Clamps.
Retarding chamber is specially designed to provide extra-large heat to dry each particle of material.
The base is specially designed to give extra strength and a vortex effect.
FBD 5
FBD 10
FBD 30
FBD 60
FBD 120
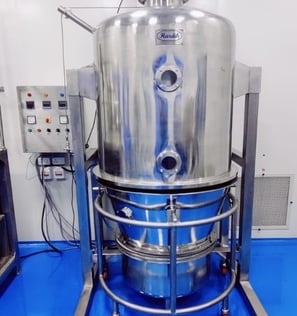
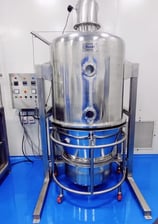
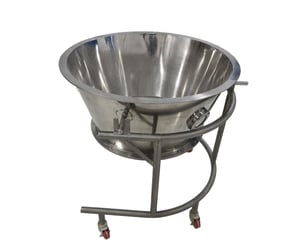
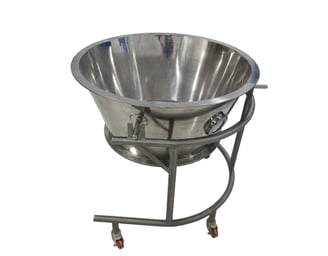
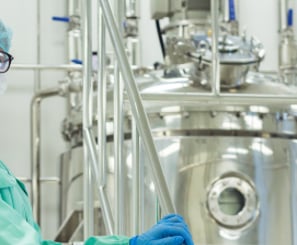
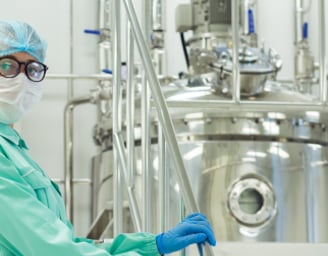
FBD 200
FBD 250
FBD 300
FBD 500
STANDARD MODELS (CAPACITY IN Kg.)
SALIENT FEATURES
RAPID MIXER GRANULATOR (RMG)
Rapid mixer granulator is used to mix the pharmaceutical ingredients and make the granules before compression and is also called a high-shear mixer. Impellers and choppers are mainly responsible for wet granulation in the rapid mixer granulator.
MAIN IMPELLER & DRIVE
The main impeller having a speed 750 / 1500 synchronous dual HP motor, connected through a belt drive to a worm reduction gearbox with chain coupling.
The main impeller provides a mixing of material at the centre and bottom of the bowl, driven through a specially designed bearing housing that provides an inside wash facility and prevents leakage of material from the bottom, resulting in a long-lasting Gearbox.
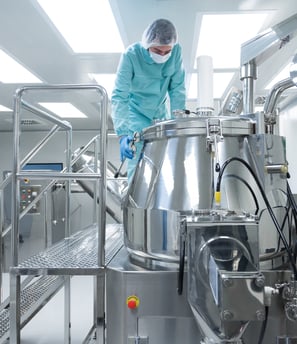
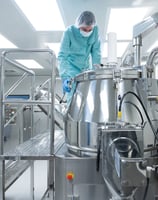
RMG can be provided with loading & unloading units to make an assembly line & reduce material handling (Optional Feature)
Main Bearing Housing provided with 3 Nos. Oil Seals and sleeve to minimize powder leakages/cross-contamination.
The main panel provided with pressure switch control for the proper functioning of the machine at desired pressure of air only to prevent powder entry into the impeller and eliminates jamming of impellers.
To eliminate powder entering the seal, Air purged shaft seals are provided.
Built-in cleaning system for both shaft seals.
Taper lock pulley on the main drive to reduce vibration and better transmission efficiency.
Chopper motor with built-in S.S. shaft to eliminate roller, bearings and reduce maintenance.
Discharge plunger provided with 3 position solenoid valve to open and close at desired levels, thereby regulating the discharge and preventing discharge of large lumps.
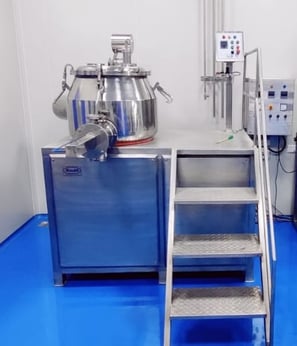
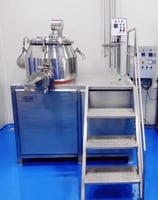
RMG 25
RMG 50
RMG 100
RMG 150
RMG 250
RMG 300
STANDARD MODELS (CAPACITY IN Liter.)
SALIENT FEATURES
OCTAGONAL BLENDER, DOUBLE CONE BLENDER
General structure made out of M.S.& colored in Standard Model.
GMP Model made out of S.S. 304 and S.S. 316 (optional) & polished to the matt finish.
Manual rotating facility with hand wheel for inching.
The Octagonal shape & slow speed gives sufficient continuous movement to the granules hence results in good quality.
Suitable for dry mixing of products in granule form.
Easy for Loading, Unloading, and cleaning of the material.
Flame-proof drive motor along with flame proof starter as an optional feature.
Cylindrical container with cone for material charging.
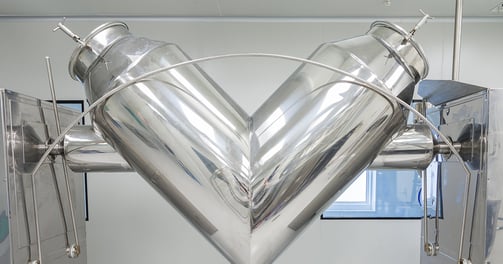
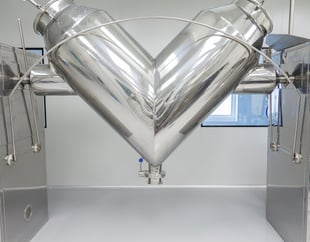
BLD 50
BLD 100
BLD 200
BLD 250
BLD 300
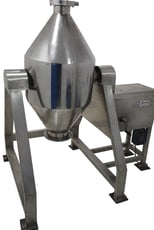
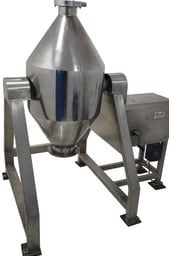
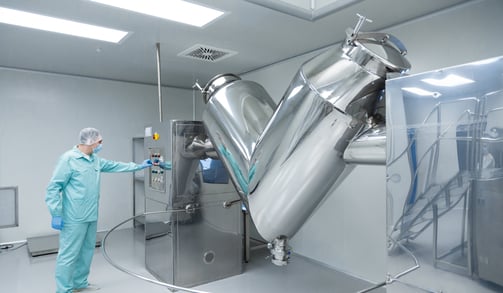
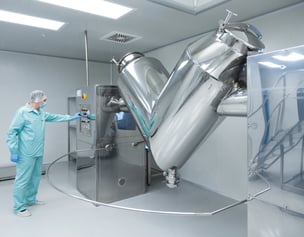
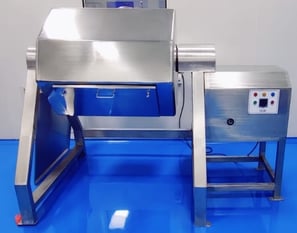
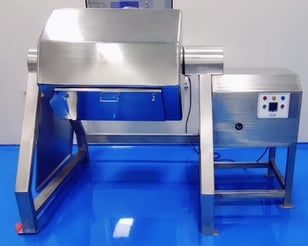
STANDARD MODELS (CAPACITY IN Kg.)
SALIENT FEATURES
BLD 500
BLD 600
BLD 700
BLD 1000
MASS MIXER
The Mass Mixer is used for homogeneously mixing of dry and wet material and especially suitable for powder, which is going to be used in Pharmaceuticals, Food, Herbals, Agro Chemicals & Chemical industries.
We designed The mass mixer with a stable fabricated structure with Electrical Motor, gearbox, Mixing-drum, Stirrer, and Tilting device. A specially designed self-adjusting sealing arrangement of unique design is provided to ensure that no black particle enters into the mixing drum. You can Tilt the Device, which gives you easy access for Unloading the Material and cleaning the Mixing.
CAPACITY : Kg./BATCH
25, 50, 100, 250
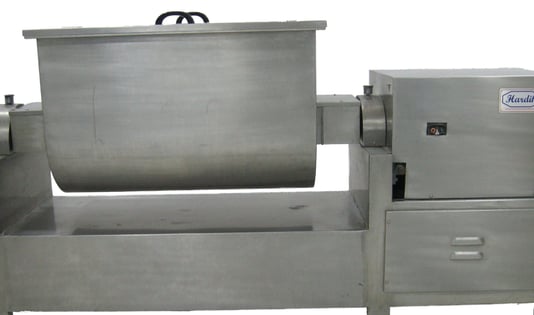
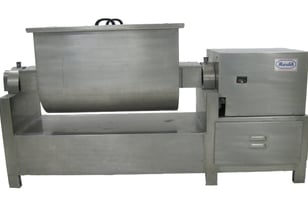
MULTI MILL
Multi Mill is used for wet and dry granulation, pulverization, shredding, chopping, and size reduction. Particle size reduction is done through impact in air, on material by blades moving at high speeds, inside a cylindrical sieve. The particles of the desired size pass out through the screen placed inside the hopper
Multi Mill is used in Pharmaceuticals, Chemicals, Cosmetics, Ceramics, Colors, Dyestuff, Food products, Pesticides, Fertilizers, Spices, Detergents, Insecticides, Plastics and Resins industries.
Output : 50 to 200 Kg/hours
(depending upon the product and reduction required in size)
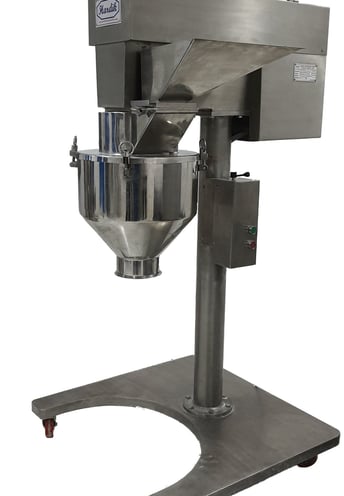
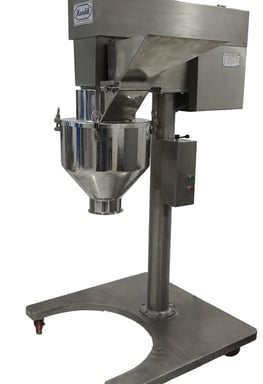
VIBRO SHIFTER
Vibratory Sifter, commonly known as Vibro shifter; is used in Sifting of materials in Pharmaceutical manufacturing with different sizes of the mesh of Sieves.
Uses of Vibro Sifter
Sifting is done to remove lumps or growth that might have formed on the materials after being stored for a longer period and materials are passed through a mesh that opens, which leads to fine the materials. It also removes the unrequired foreign particles and separate the materials according to size.
Standard Sizes : 20", 30", 36", 48", 60"
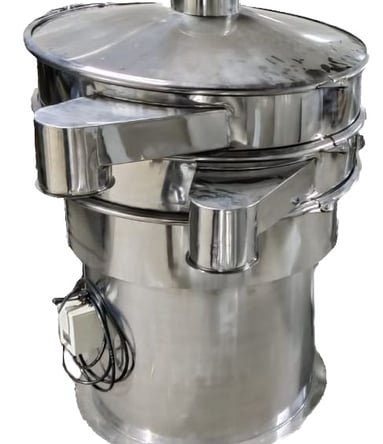
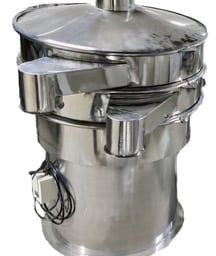
Rotary Tablet Press Machine
Paint free Tablet Manufacturing Zone
Lower Guards of Polished Stainless Steel
Upper Guards of transparent Acrylic material
Electronic / Digital, Tablet cum RPM Counter
Aluminum turret guards
Higher turret speed 17 to 40 RPM
Phosphorous Bronze Bush provided inside the turret hole
Imported Needle Roller bearing provided at the bottom of turret
Cam tracks & pressure rolls made out of alloy steel
Worm is made of Phosphorous Bronze material
Separate grinded Center Pillar of M.S. material
Upper punch penetration system
Effective Dust Extraction Nozzles
Inter Lock Switches to all Guards
Variable Speed Pulley
Disc type Friction Clutch Start System
One Shot Lubrication System
Double Sided Lifting Cams
Overload Pressure Release System
Reverse direction motion protection is provided to avoid a major accident
3 Piece Turret can be supplied with oil groove on top face of turret for collection for excess oil
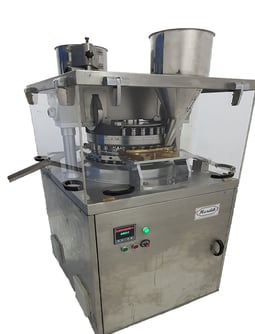
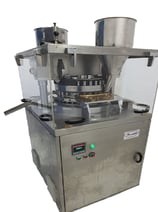
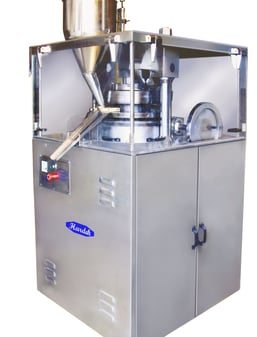

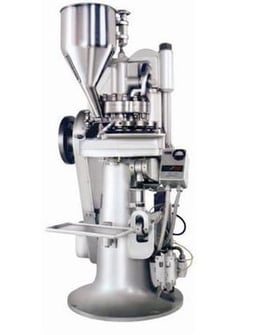
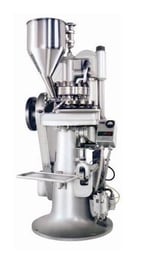
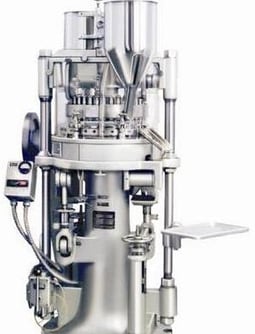
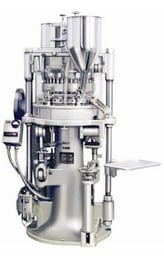
GMP & Non GMP Models
SALIENT FEATURES
The tablet compression machine makes the tablets by pressing the granules in the die with a lower and an upper punch. Tablets are being formed by compressing the granules using compression machines. A tablet formation takes place by the combined pressing action of two punches and a die.
How Tablet Compression Machine Works?
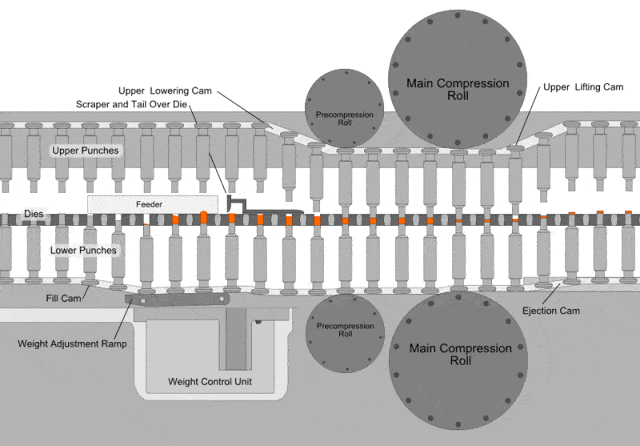
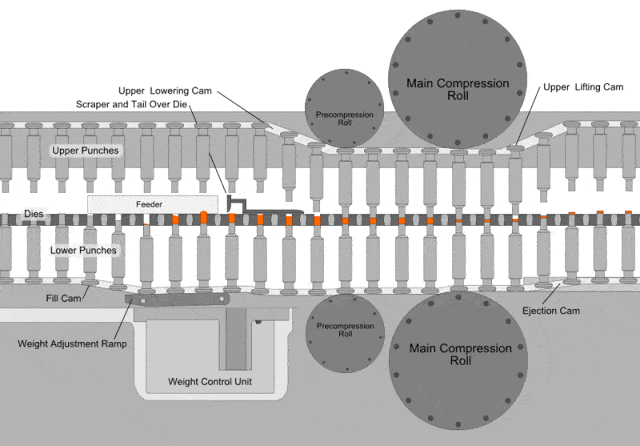
TABLET COATING MACHINE
Tablet costing machine is ideal for film and sugar coating. The machine is designed with a fabricated structure fitted with an SS enclosure and drive unit of motor and reduction gearbox with Variable Speed Drive to achieve 5 to 15 RPM by variable speed pulley.
A hot air blower system is provided separately on a trolley for easy cleaning and setting.
Sizes: Coating machine is available with 12" to 48"size of SS Coating pan.
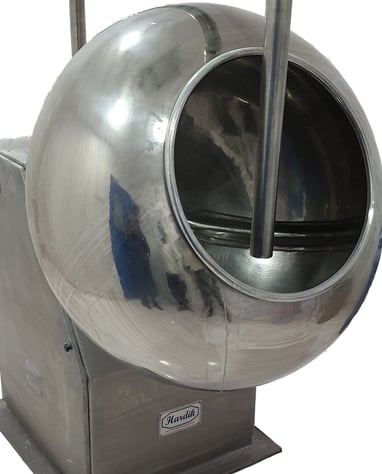
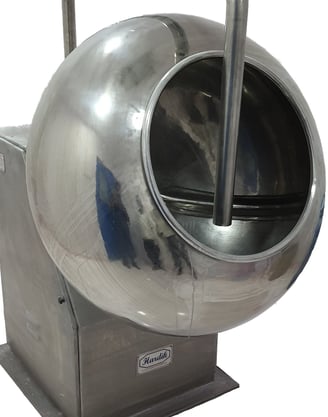
De-Burring & De-Dusting
SALIENT FEATURES:
Noiseless & Maintenance free unit.
A brushing Unit is provided for better results in cleaning the tablets.
All contact parts made of stainless steel and components can be easily washed and/or sterilized.
The tablet conveying route is so geometrically designed for the arrangement of the tablets on their burrs which can break easily.
Efficient de-burring & de-dusting, the full suction output is concentrated on the De-dusting zone for flushing out powder.
Output: 5000 to 2,50,000 Tablet / Hour
Dust Extractor
SALIENT FEATURES
Provided with stainless steel SS 304 contact parts.
Minimizes mechanical strain, excessive wear of tableting machine - resulting in minimum machine break-downs and punch wears.
All inlet manifolds and dust collection trays are of S.S.
PVC flexible hoses are plain, i.e. without grooves, from inside for ease in cleaning.
Four inlet manifolds facilitate connecting Cip Press Machine and two De-dusting units.
Suction capacity: 300 CFM,
Customization as per clients' requirements is possible.
Looking for Something Specific?
Didn’t find the manufacturing capability you’re looking for?
Don’t worry—Verkora’s extensive network of expert manufacturers is built to adapt to your unique requirements. Whatever the complexity or scale, we’re here to ensure you receive the right components and solutions tailored to your needs.
Let’s create something extraordinary together!
Follow us on Social Media
Contacts
+91 9724144144
+91 9601451802
info@verkora.com
Address
Verkora Private Limited
528, The Nikol Trade Centre - TNTC, Nikol, Ahmedabad 382350, Gujarat, INDIA
Manufacturing
Empowerment
Fulfill Need
Grow
Connect
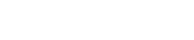
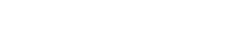